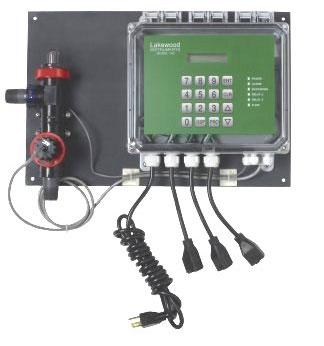
Advanced Cooling Tower Management: Enhancing Efficiency with Lakewood Model 140
February 28, 2024 0 Comments
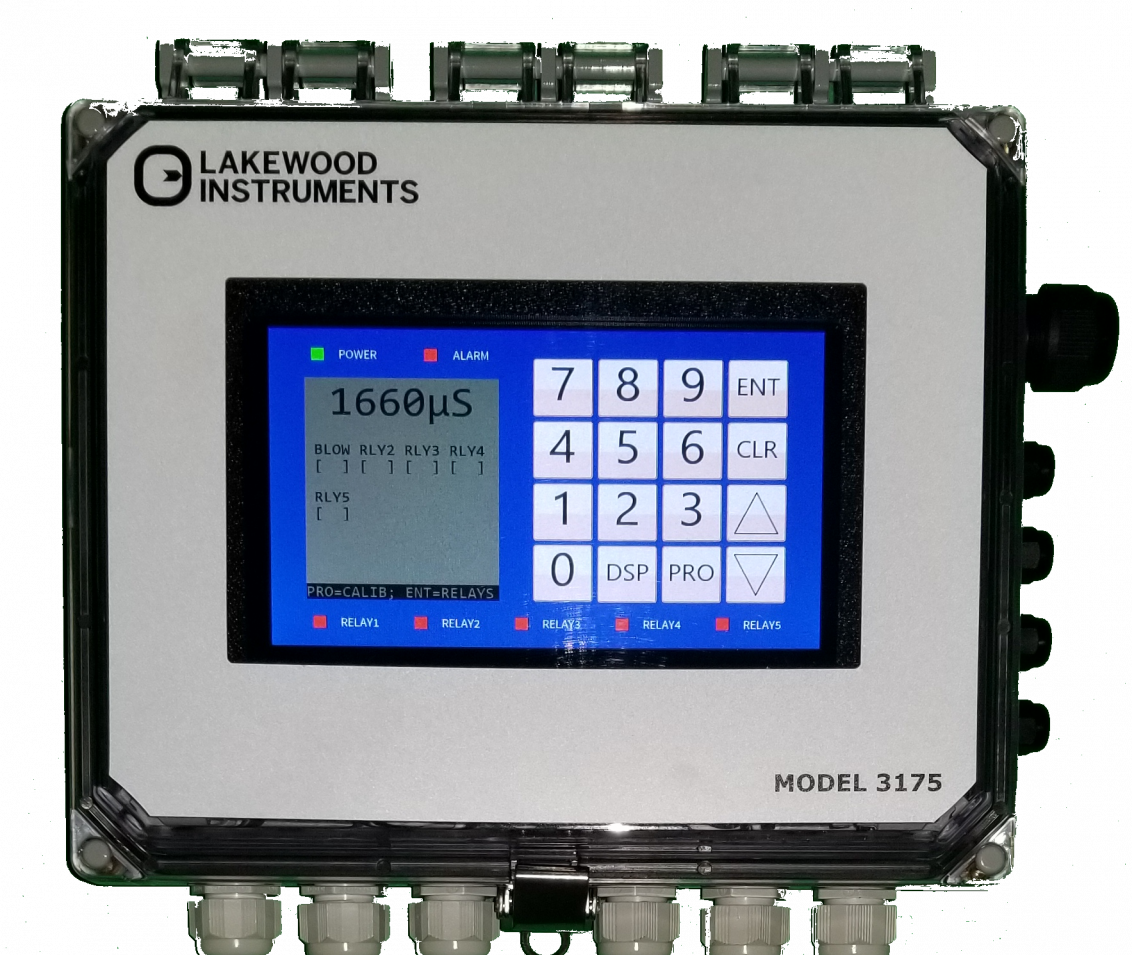
Optimizing Cooling Tower Performance: Understanding Efficiency, Maintenance, and Water Quality Management
February 28, 2024 0 Comments
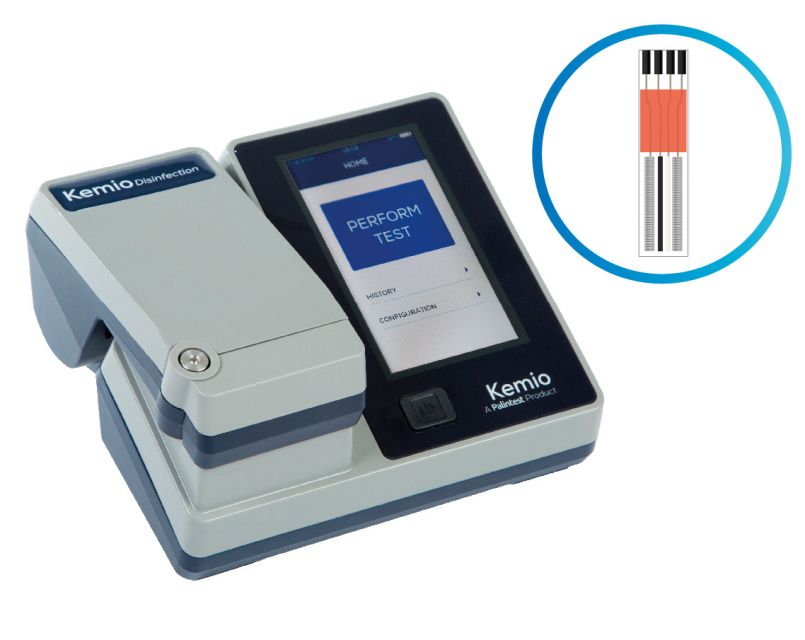
Revolutionizing Water Analysis: Everything You Need to Know About the Kemio KEM10DIS
April 19, 2023 0 Comments
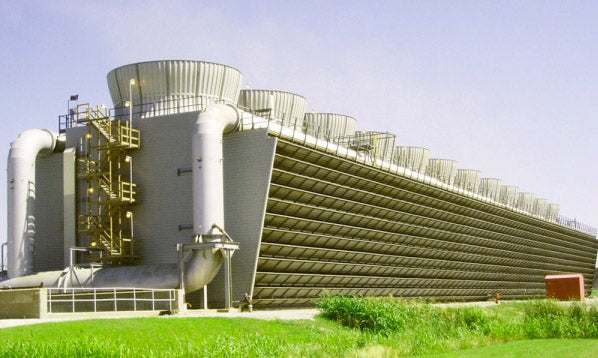
Optimizing Cooling Tower Performance with Conductivity Controllers
April 17, 2023 0 Comments
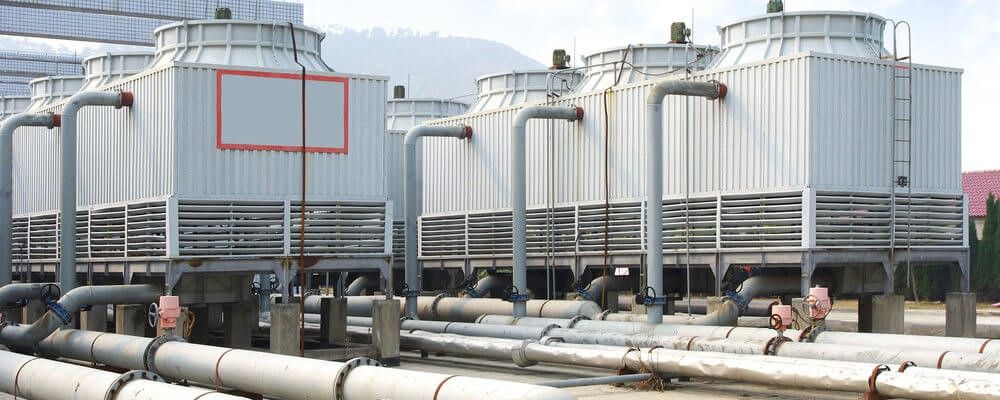
Avoid this issues when starting a cooling tower
March 20, 2023 0 Comments
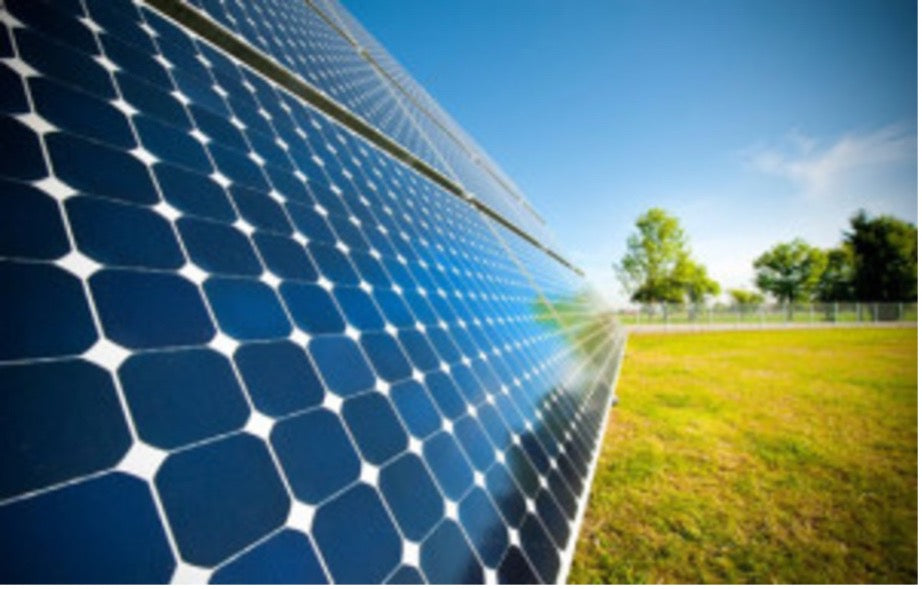
Basic solar energy system
May 18, 2021 0 Comments
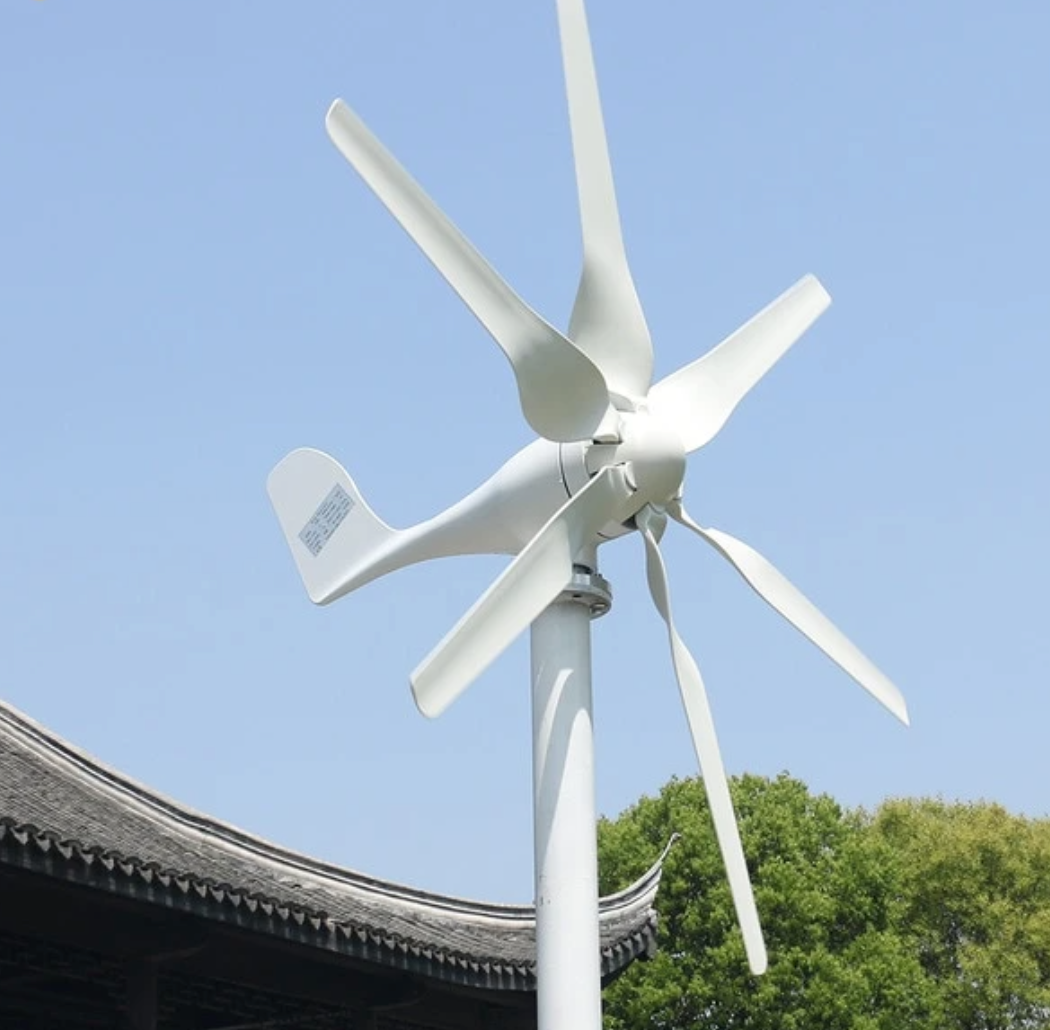
How do wind turbines work?
May 12, 2021 0 Comments

What is water TDS?
May 06, 2021 0 Comments

What is Ozone ?
April 28, 2021 0 Comments
Most people have heard of ozone thanks to media coverage about pollution and the ozone layer. But for many, that is where their knowledge ends. The first thing you should tell a homeowner is that ozone is nothing more than O3—three oxygen atoms bound together.
That extra oxygen atom wants to hook up with other material, like unwanted microorganisms in water filtration systems. For the purpose of disinfecting water, ozone comes in contact with contaminants and pathogens that can damage equipment and get in the water supply. The extra oxygen atom oxidizes the contaminant and the O3 becomes O2—just plain old oxygen.

Does Ozone kill viruses ?
April 28, 2021 0 Comments
It was shown that after 30 seconds of in vitro direct exposure to ozone, 99 percent of the viruses are inactivated. Although this evidence is of considerable importance, outside of the laboratory models, there are various parameters that influence the time required to obtain the same result. First of all, it was seen that the inactivation of 99% of viruses by ozonation requires its spread at concentrations higher than those necessary for the bacteria. A longer exposure time, about 30 minutes, is necessary for the treatment of the surfaces of the environment (surface viruses), while for any viral particles suspended in the air (airborne viruses) 8-10 minutes are enough to remove 99.9% of them. Viruses in water are more susceptible to ozone inactivation and short contact time, about 1 min or little more, are sufficient to inactivate 99% of them.
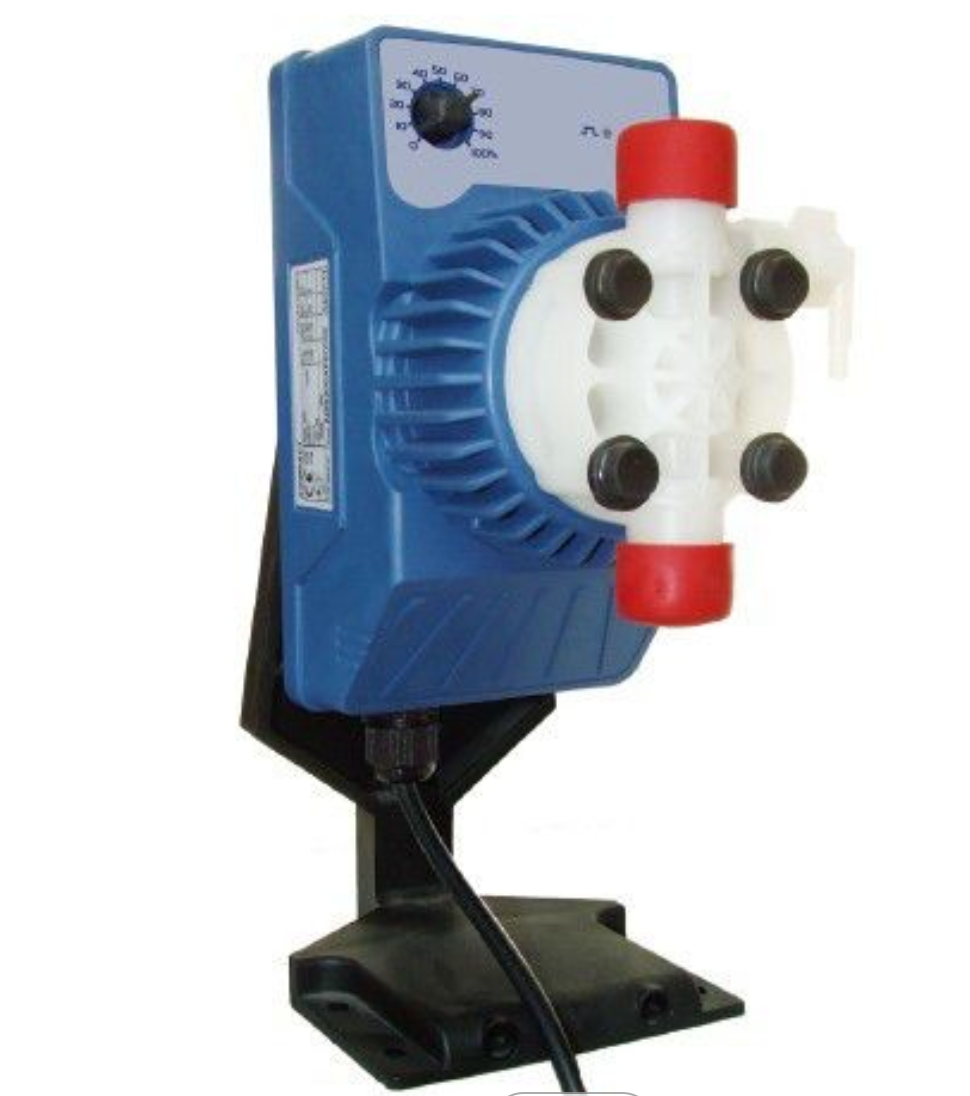
Why do I need a metering pump?
April 27, 2021 0 Comments
A positive displacement pump moves a fluid by repeatedly enclosing a fixed volume, with the aid of seals or valves, and moving it mechanically through the system. The pumping action is cyclic and can be driven by pistons, screws, gears, lobes, diaphragms or vanes. There are two main types: reciprocating and rotary.Positive displacement pumps are preferred for applications involving highly viscous fluids such as thick oils and slurries, especially at high pressures, for complex feeds such as emulsions, foodstuffs or biological fluids, and also when accurate dosing is required.
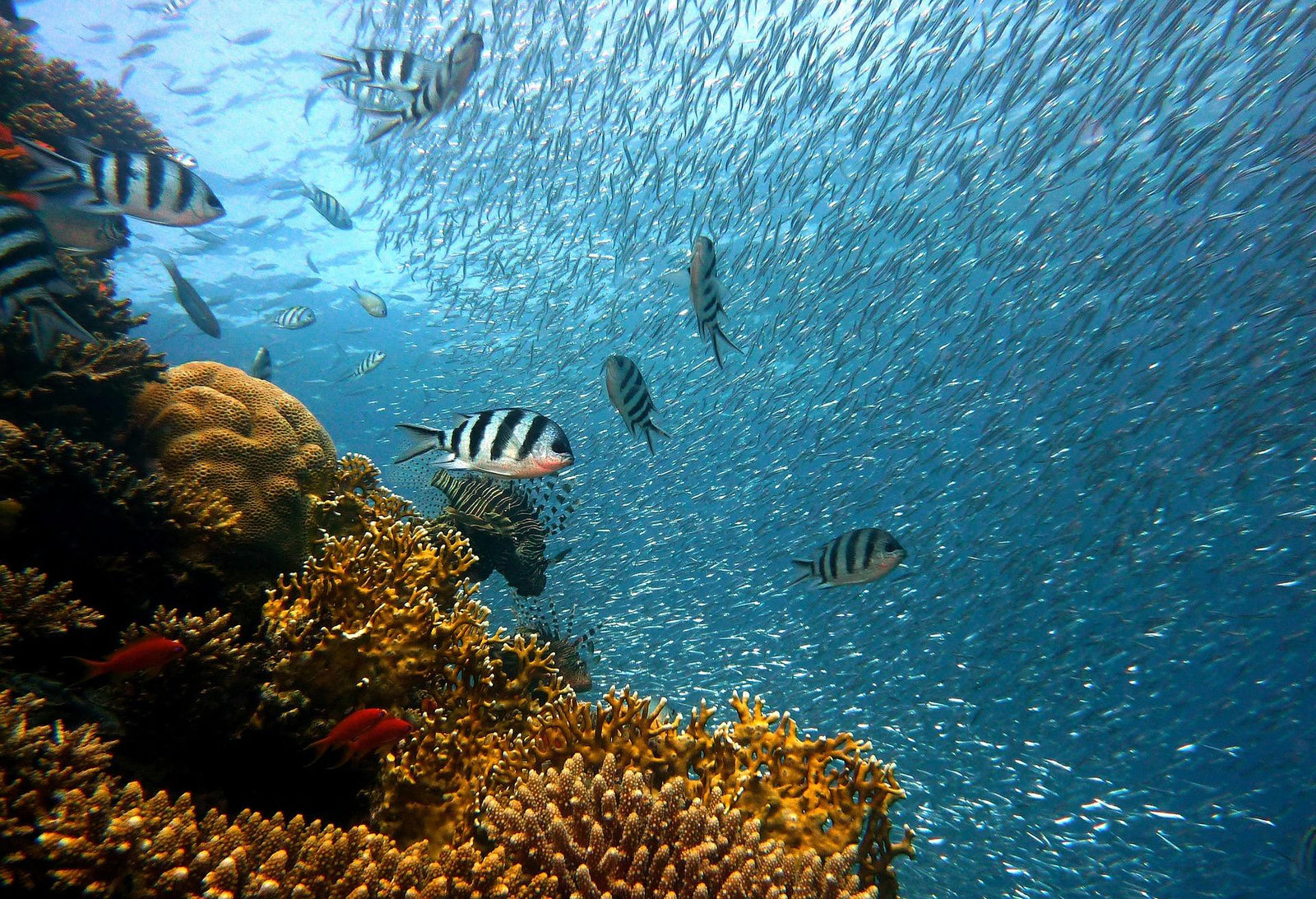
Water Conductivity
April 20, 2021 0 Comments